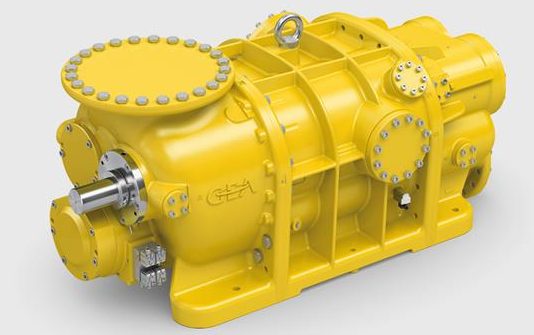
In case you’re running one of the 140 working refineries in the UAE, the exact opposite thing you need is a spontaneous shutdown. Be that as it may, a creation halt is actually what is in danger on the off chance that you don’t watch out for the consistency of the lubricating oil utilized in any of the rotational blowers in the plant, with the most elevated danger of these being the gas blowers. One minute all procedures are fully operational, and the following there’s a bearing disappointment and creation stops.
It’s not simply the expense of lost creation, either – a blower disappointment in a single piece of the refinery can keep running in the many thousands per day in lost income, comparative adds up to remake a blower, and countless dollars for a substitution – also the sunk expense of maintaining saves.
Plainly managing grease consistency is basic to maintaining blower wellbeing, yet it is basic practice to screen oil thickness in each real blower once every month by sending an example to a lab for testing. For blowers where grease interacts with methane and other light hydrocarbon gases, the ointment’s thickness can separate substantially more rapidly, increasing the danger of disappointment. Through hard karma, refiners additionally have discovered that ongoing temperature monitoring is inadequate to screen oil consistency.
A noteworthy Gulf Coast refinery engineer indicates they tackled the issue by moving to constant monitoring of lube oil thickness in the basic blowers. “We perceived that in-line viscometers are the most ideal approach to recognize what is befalling the lube oil in our enormous screw blowers,” says the plant administrator. “Further, we have found in-line grease thickness monitoring offers a financially savvy approach to monitor blower wellbeing.”
The genuine proportion of the wellbeing of a grease’s thickness must be checked when estimated in situ with gas vapors broke up in the ointment. Further, monitoring ointment temperature isn’t adequate to secure blower bearings, particularly in applications where procedure begins and stops can happen.
What’s required is in-line thickness monitoring to help furnish plant administrators with constant information on oil consistency. There is an answer for refinery administrators working to keep plants online and producing. New, inexpensive and rough in-line viscometers can screen continuous changes in ointment consistency, offering a practical method to monitor blower well being progressively.
Refineries and blowers
Rotational blowers are utilized all through lubricants in UAE in applications ranging from vapor recuperation to gas processing activities. Screw and parchment blowers make up a noteworthy segment of this hardware.
Screw blowers utilize two corresponding screws to pack gases. Gas is nourished into the blower by suction and traveled through the strings by the rotating screws. Pressure happens as the leeway between the strings diminishes, forcing the compacted gas to exit toward the finish of the screws.
Parchment blowers utilize two interleaved winding vanes to move and pack liquids and gases. Normally found in intermediate and finished result applications, scroll blowers are esteemed for unwavering quality and smooth task.
The significance of grease consistency
In the two kinds of blowers, lube oil is utilized to seal the blower from gas spills, grease up moving parts and oversee temperature during task. The state of oil is a basic factor in extending a blower’s bearing life and by and large unwavering quality. Monitoring and managing grease consistency can counteract exorbitant breakdowns because of bearing disappointment. Thickness likewise assumes a job in vitality productivity – interest for progressively effective blowers is driving the utilization of lower-consistency lubricants.
A scope of lube oils, commonly engineered in synthesis, is accessible for use in blowers. Water opposition, warm dependability, long life, protection from oxidation and protection from ingestion of procedure gasses are significant attributes. While the objective is an oil with a long helpful life, unforgiving situations, contaminants and even stickiness in the refinery’s outer condition can incredibly lessen lube oil’s useful life expectancy.
Monitoring lube oil thickness is the most ideal approach to anticipate bearing wear and counteract blower disappointment. While a few plants may screen as infrequently as once every month, quick changes in thickness occur – and the outcomes can be serious.
Changes in consistency – and ensuing dangers
Blower lube oils are planned to function admirably and remain stable at high temperatures and weights. Hydro-treated mineral oils are utilized for their low gas dissolvability (1-5 %.) Synthetic blower Oil (PAO, PAG) are utilized depending on the procedure and how much gas weakening is available. PAO (Poly Alpha Olefin) oils, for instance, have amazing water obstruction and protection from oxidation; PAG (Polyalkylene Glycol) oils, which don’t promptly retain gasses, are utilized in applications where procedure gases are compacted.
Numerous components can influence lube oil consistency. These include:
- Oxidation – caused when churning lube oil froths, exposing more oil to surface air and causing oxidation that brings down consistency and undermines helpful ointment life.
- Bubbles – as foaming oil agitates against the screws or vanes of the blower, bubbles structure, instantly dropping the thickness of the oil.
- Dilution – caused when the hydraulic oils in UAE is weakened with gas, for example, methane, and dropping thickness.
- Contamination – vapors from hydrocarbons being prepared can blend with lube oil. This light hydrocarbon and methane contamination – one refinery supervisor calls it ‘a witches’ mix’ – makes measuring thickness challenging.
- Temperature change – normally at start-up, critical changes in temperature can happen that influence the consistency of the underlying lube oil just as any contaminants, further aggravating circumstance.
A scope of blower disappointments can result: bearings, both rotating and push, can come up short, which in turn causes wear on the rotor gathering. Replacing bearings is less expensive than an absolute modify or substitution; in any case, the plant faces personal time.
The unconventionality of thickness change implies month to month consistency checks are insufficient to forestall bearing disappointment and consequent plant personal time. Some blower clients are designing in-line viscometers into blowers to screen ongoing changes in consistency that occur between standard oil lab examinations, viewing this ‘deterrent’ approach as a perfect method to guarantee bearing life and minimize the expenses related with unscheduled personal time.
Procedure viscometer approaches
Not all procedure viscometers are made equivalent. Cambridge Viscosity instruments, for instance, utilize an innovative sensor innovation that uses an oscillating cylinder and electromagnetic sensors. Different procedure viscometer innovation methodologies include falling cylinder, falling circle, glass-slender, U-cylinder, and vibration structures.
In all cases, plant chiefs should search for the following attributes for in-line oil consistency estimation:
- Menu-driven electronic controls are ground-breaking and simple to utilize.
- Self-cleaning sensor – using the in-line liquid to clean the sensor while it is taking estimations decreases unscheduled maintenance.
- Built-in temperature recognition – the sensor should demonstrate temperature as a simple reading
- Multiple yield signals – the sensor should show temperature and temperature-repaid thickness readings.
- Automatic consistency control – search for a sensor that is pre-set however reconfigurable. The sensor ought to have the option to ‘realize’ how much control is required for every liquid setting.
- Data logging – date and time-code ought to be consequently logged, creating a review trail and simplifying execution and quality pattern estimation.
- Security and cautions – intended to avoid unapproved changes and sound alerts when setpoints are come to so administrators can make a move rapidly.
· Quick-change memory settings – for procedure lines that run more than one liquid, this element rearranges changing settings.